Metalworking machinery requires a high level of control, technical accuracy, and compliance with safety measures. Since many industries use precision metalworking for fabrication and production, following the proper safety measures is necessary. Because of the operation of large and powerful machines, the use of metalworking equipment calls for procedural knowledge and adherence. Here are the safety protocols for operating metalworking equipment:
Recognizing the Functional Design of the Metalworking Equipment
There are many types of mechanical systems employed in metalworking, and they vary depending on their use. They also vary based on the material being worked on and the production capacity of the system. These include press brakes, CNC machines, shears, grinders, and lathes, all with mechanical hazards. One of the initial and significant measures towards safe operation entails becoming acquainted with the physical characteristics of the equipment.
Visibility, controls, and stability of the working surface are the major factors that define usability. Operators should be familiar with the layout of the moving parts, tool path tolerances, and emergency stop procedures. Understanding the position of the machine guards, how feed mechanisms work, and the sequence of operations reduces the likelihood of an operator making a mistake.
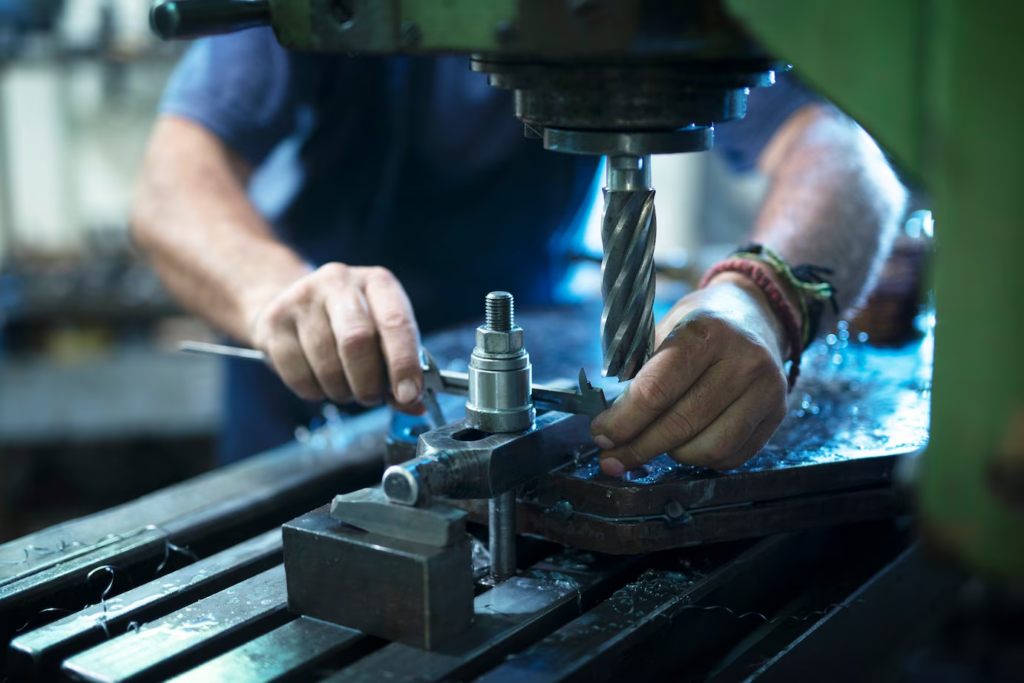
Maintaining Operational Readiness Through Inspection
Before any machine is started, it should undergo a series of checks to confirm that it is ready for use. This might involve checking hydraulic lines, tooling alignment, electrical enclosures, and lubrication points. Identifying problems early, such as vibrations, unexpected resistance, or faulty sensors prevents the development of major mechanical issues.
Regular inspections also help to validate the effectiveness of the machine guarding and interlock systems. Fixed and adjustable guards must be properly secured and positioned, and any control devices should be checked to confirm that they effectively isolate the machine during maintenance. The documentation of the inspection results helps to provide a trail that makes the accountability process more tangible and also confirms that the feedback loop is effective in enhancing the safety of the machines.
Establishing Clear Machine Control Procedures
The foundation for the safe operation of the machines lies in well-established control measures. These measures include setting the machine to a secure mode during setup, checking the zero-energy states when changing tooling, and checking alignment before running automated sequences. Control procedures should outline the sequence of actions and define the distribution of control tasks among the team members. Remote-control systems and operator panels should be positioned to optimize visibility and accessibility. This increases situational awareness and makes it possible to respond to emerging issues promptly. Implementation of start-up warnings and audible signals enhances safety by informing the operator that the machine is on and if there is an issue.
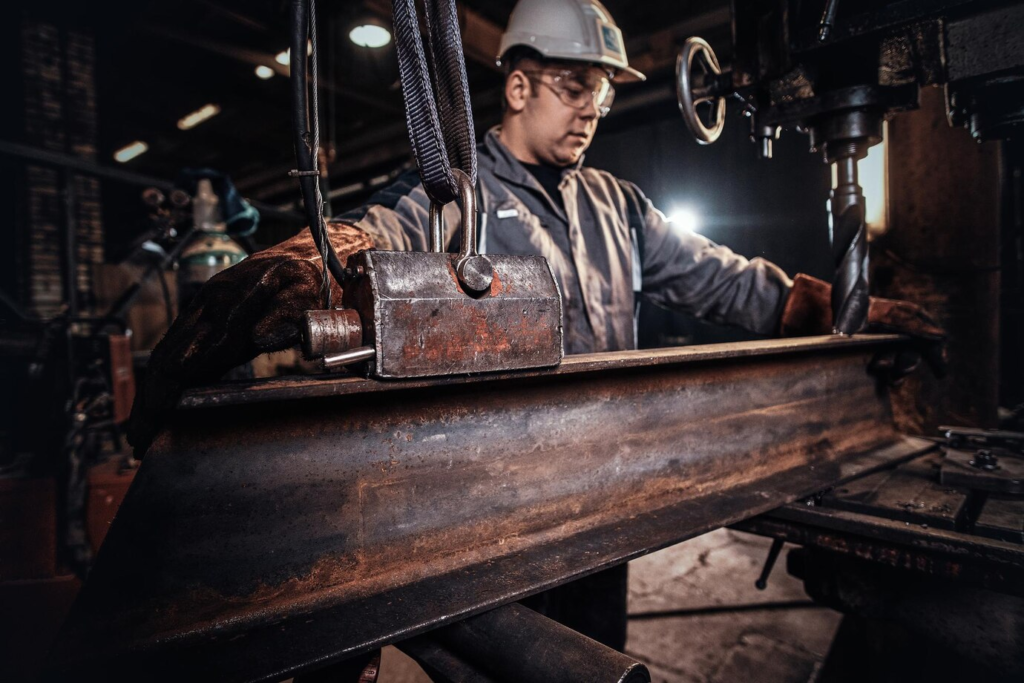
Using Material Handling Systems Appropriately
In a metalworking facility, confirm that the material flow is safe. The flow and handling should be deliberate when conveying stock into the CNC equipment or retrieving the finished components from presses. Load-lifting equipment, including jib cranes, conveyors, and automated transfer devices, should be run with the machine cycle. Be precise when positioning raw materials. Misalignment during feeding or tool engagement can damage metalworking equipment and create unsafe working conditions. Proper clamping, fixturing, and support minimize the amount of handling required. It also reduces the risk of coming into contact with pinch points.
Wearing the Right Protective Clothing and Equipment
Personal protective equipment should be chosen according to the requirements of the particular metalworking operation. Safety glasses, goggles, and protective masks protect the face and eyes from debris and splinters. Gloves are required because of the possibility of flying debris, sparks, or tool fragments. Besides personal protective equipment, the clothing worn should also be safe. Loose clothing, rings, or loose hair can be dangerous around rotating equipment.
Purchase a Metalworking Equipment
Select the right supplier if you work with machinery designed for performance, durability, and compatibility with your operations. When assessing equipment, look at the machine’s capacity, the level of control, integration, and compatibility with safety measures. When you buy your equipment from a partner who provides more than just the equipment but also knowledge and assistance, you set your operation up for long-term success and lower risk. Contact top suppliers to learn more about the available systems if you require metalworking equipment.