High Density Interconnected Printed Circuit Boards, technically referred to as HDI PCBs, have become a major part of the products over time. They have become more popular among PCB designers due to various features i.e. compact size, higher density of components, better reliability and enhanced performance. Different from the regular PCBs due to the product layout, the HDI circuit boards are designed, manufactured and assembled with highly skilled and latest processes. In case of a deviation from the standards practices, the end product will have some serious issues with quality & reliability.
What is HDI PCB?
HDI PCB is one kind of PCB that has more compact routing and smaller spaces between components. This PCB can extremely reduce the volume of PCB, making it the best choice for portable and sophisticated devices.
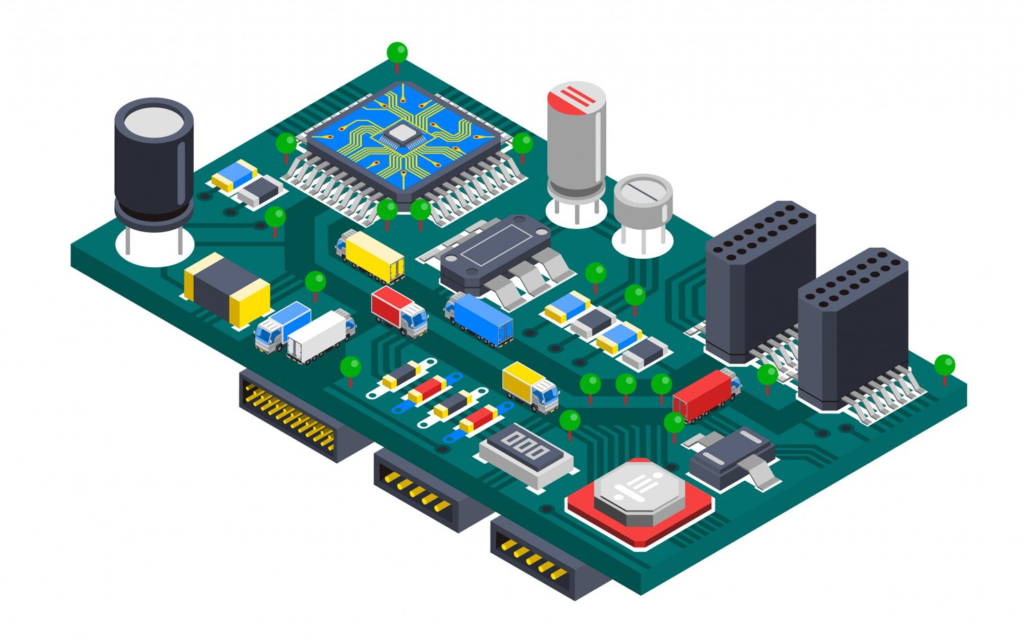
Some of the Frequent Issues in HDI PCB Manufacturing
Each PCB is designed and produced with reference to a specific electrical & electronic circuit layout. Based on the design data, there may be some adjustments required during the PCB manufacturing and assembly stages. However, some of the key steps remain the same in each version. Those common steps & processes have few errors & defects that can be found during the complete HDI PCB manufacturing process.
Product Definition and Requirements – Behind every product to be designed, there lies a basic idea or requirement that acts as a base for further discussions and analysis. Based on these, further product definitions and features are finalised with reference to initial requirements. All these details are needed to be perfectly fixed without leaving even a minor error. All the further tasks and activities are planned and carried out on this initial detail only. Any mismatch in this information will definitely end in a wrong or undesired product.
Inadequate Design and Layout Preparations – After receiving the end requirements and product features, the initial design phase starts. All the product and PCB parameters, raw material details, manufacturing & assembly instructions and quality points are also prepared along with the PCB design data. Any kind of misinformation while preparing the design layout and database will lead to major defects in the end PCB product.
Raw Material Characteristics & Quality – Any manufacturing process requires raw materials that need to be processed at further stages. During design data preparation, the detailed bill of materials (BOM) is also prepared for further production release. This contains the complete information about the raw material type, quantity, make, version, class, and source. For each component, there may be multiple varieties available in the market with numerous suppliers. Selecting the best supplier for raw material procurement becomes crucial for any PCB production. Limiting the quality of raw materials by looking at prices and availability makes a major impact on the quality of the finished product even during the end application phase. Each raw component contributes to the product quality significantly. PCB manufacturing often makes mistakes in raw material and supplier selection to meet the project timelines and profit margins.
PCB Assembly Process – PCB manufacturing and assembly is itself a technical approach which includes several steps. All the processes are lined up in a defined and logical manner to get the desired product output. Each step has its own parameters defined during the setup installation and also during the PCB design data. The manufacturing instructions need to be followed carefully to produce a high-quality HDI circuit board. Skipping any part or process at any stage of PCB manufacturing and assembly affects the quality of the end product.
Insufficient Quality Checks and Testing – Quality checks are established at the required levels of the HDI board manufacturing and assembly process. Since the PCB assembly is a defined & specific approach and identifying the defects and issues in end products becomes complex after the completion of the projects. In order to get accurate defect causes and errors, the product quality is checked at various production stages. End PCB testing is also done to ensure product specifications are met. In the absence of proper quality checks and testing, the HDI circuit board will definitely have a higher chance of issues and defects.
The Basic Action to Avoid Common Mistakes in HDI PCB Manufacturing
Product quality is always a prime concern for the customers. It reflects the level of excellence of the PCB manufacturer and its capability to deliver high-end products. Here are some ways to reduce failure in HDI circuit board manufacturing.
- Planning Design and Layout for the Best Performance: HDI PCBs usually contain higher density, complex layer stackup structures and smaller spaces between components. Specific related design considerations should be complied with to confirm if the circuit board layout, routing and component placement are properly placed according to their functions. All these measures decrease the probability of circuit defect.
- Rational Design of Vias Structure: Buried and blind holes should be correctly deployed in the PCBs. The deviated holes on the PCB, especially the size of microvias, should be limited to the specified limits. Meanwhile, the drilling position of holes should be accurately controlled by the drilling machine to avoid circuit breaks and open circuits.
- Material Choice: Choose HDI technology-compatible PCB materials to fabricate the PCB. The use of good-quality materials can sharply reduce signal loss and impedance mismatch.
- Strict Checking and Approval: The assembled circuit boards must be the ones which go through rigorous electrical and mechanical testing to give the least chance of the circuit defect. Simultaneously, all the circuit boards should undergo automatic and manual inspection processes to ensure no existing defective products.
Conclusion
The HDI PCB design and manufacturing process is a highly skilled and technical approach to deal with. From the initial design stage to further PCB manufacturing and component assembly, each step is crucial for PCB manufacturers. Any defect, deviation or error during any stage will definitely have a serious impact on product quality and reliability. All these factors must be addressed carefully while working with HDI board manufacturing projects. The future of PCB manufacturing will experience many major advancements in technology and HDI circuit boards will be incorporated with various features. More productive manufacturing and assembly processes will also be part of the future HDI board manufacturing process. Some emerging techniques may affect printed circuit board manufacturers so they should catch up with the upgrading pace to fabricate the ideal PCB for customers.